Say No to 80/100
So you know it's never an easy job to make plushes.
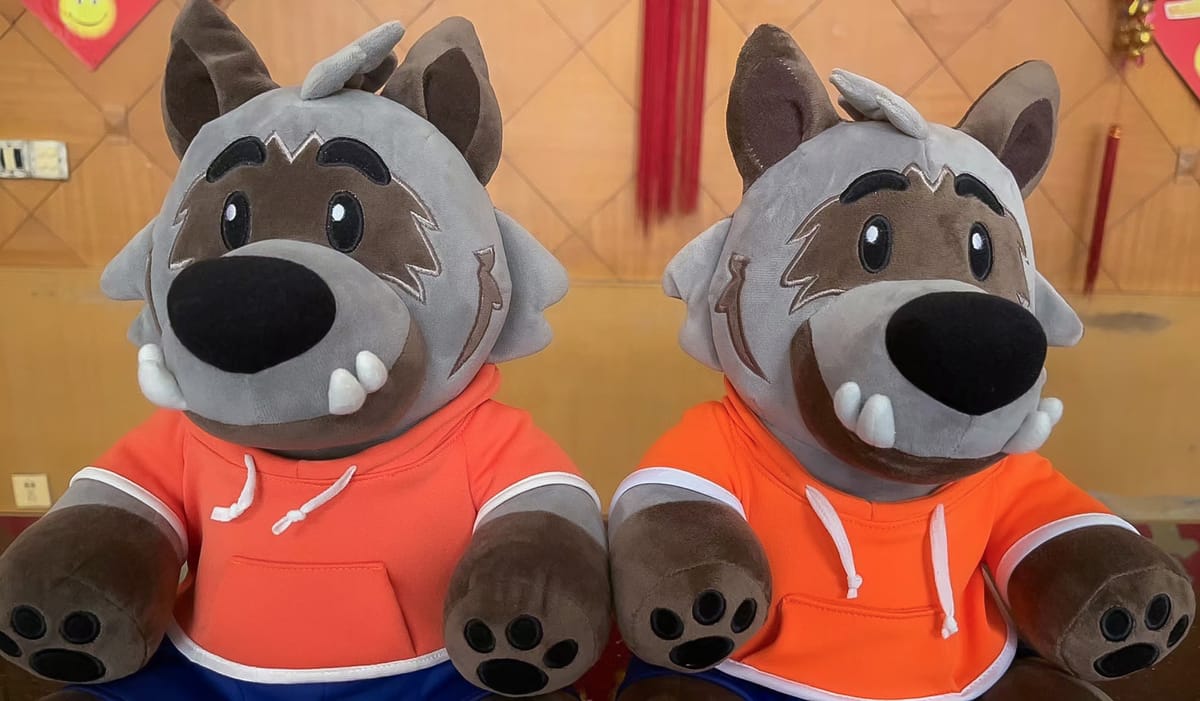
As we approach the production of our delayed plushies, we want to share some behind-the-scenes stories.
It all began with the contract breach earlier this year. Simply put, the factory faced significant losses (or so they claimed) from the low acceptance rate of previous batches (the TSR pawbs and an upcoming product). This led them to halt further production, putting their business partner—and our contractor—in a tough spot. Nonetheless, the question remained: how do we resume production swiftly?
Post-incident, we connected with two reputable manufactuers, through our connections with other suppliers. We sent work to them in parallel, not only because we're in a hurry but also to have an immediate backup in case one of them fails—let's hope they don't fail simultaneously. One of them is now working on Dave and another is working on Axel. Concurrently, we engaged our garment maker (for our T-shirts, kigu, and daki) to tailor their outfits to human clothing standards—a challenging feat for typical plush manufacturers but a resounding success for our skilled clothier.
Both manufacturers initially met "ordinary standards" with their first iteration, but we strive for excellence. Drawing from past experiences, we involved ourselves in every detail of the production process.
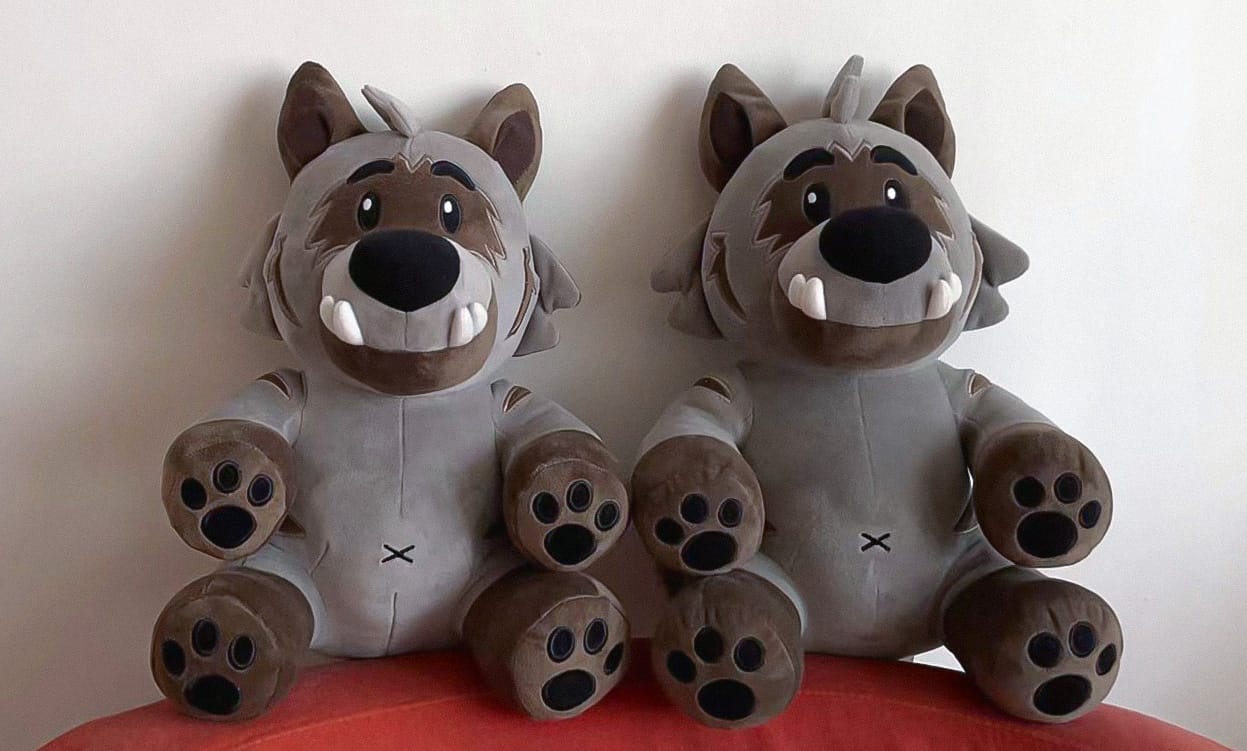
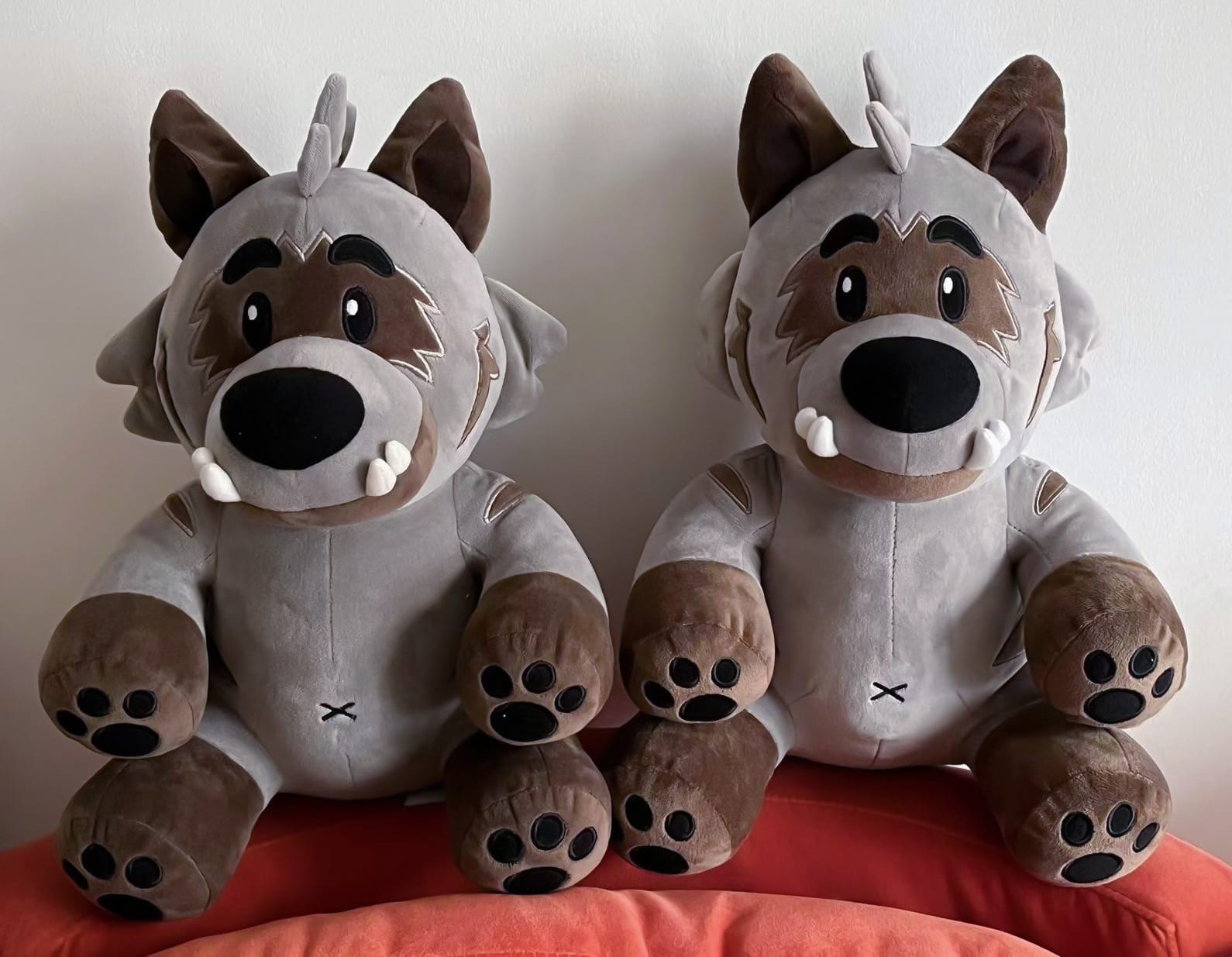
Dave New Pre-Production Sample v1.0 and v2.0, comparing to our prototype
A critical aspect is stuffing. Slight variations in fabric can drastically alter a plush’s appearance, with common issues at the joints or a flattened muzzle top. Dave 1.0 had some classic stuffing problem, but significant improvements were made in the second iteration. With plans to refine the stuffing material, we anticipate a third iteration by the end of June. Successful samples will greenlight production.
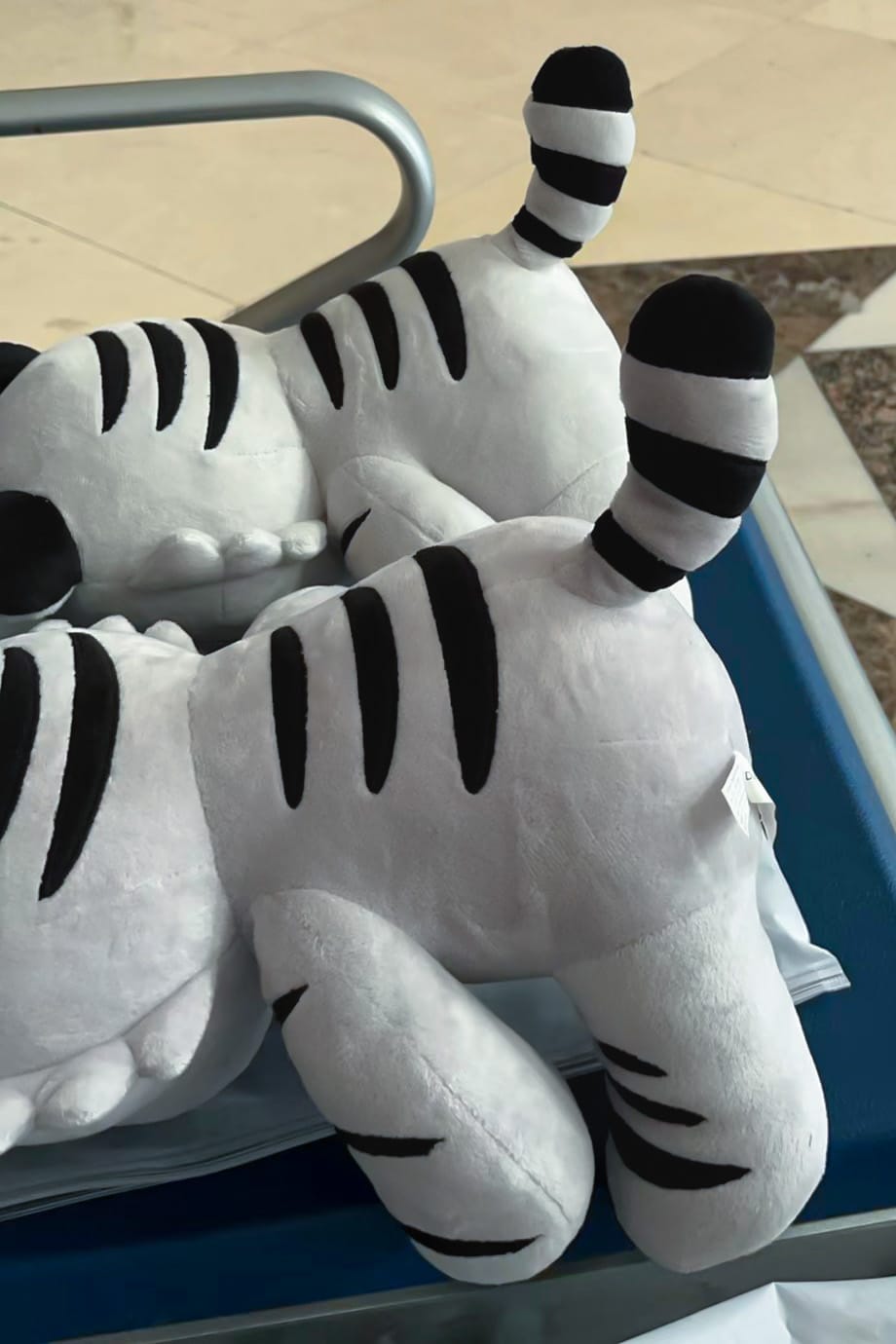
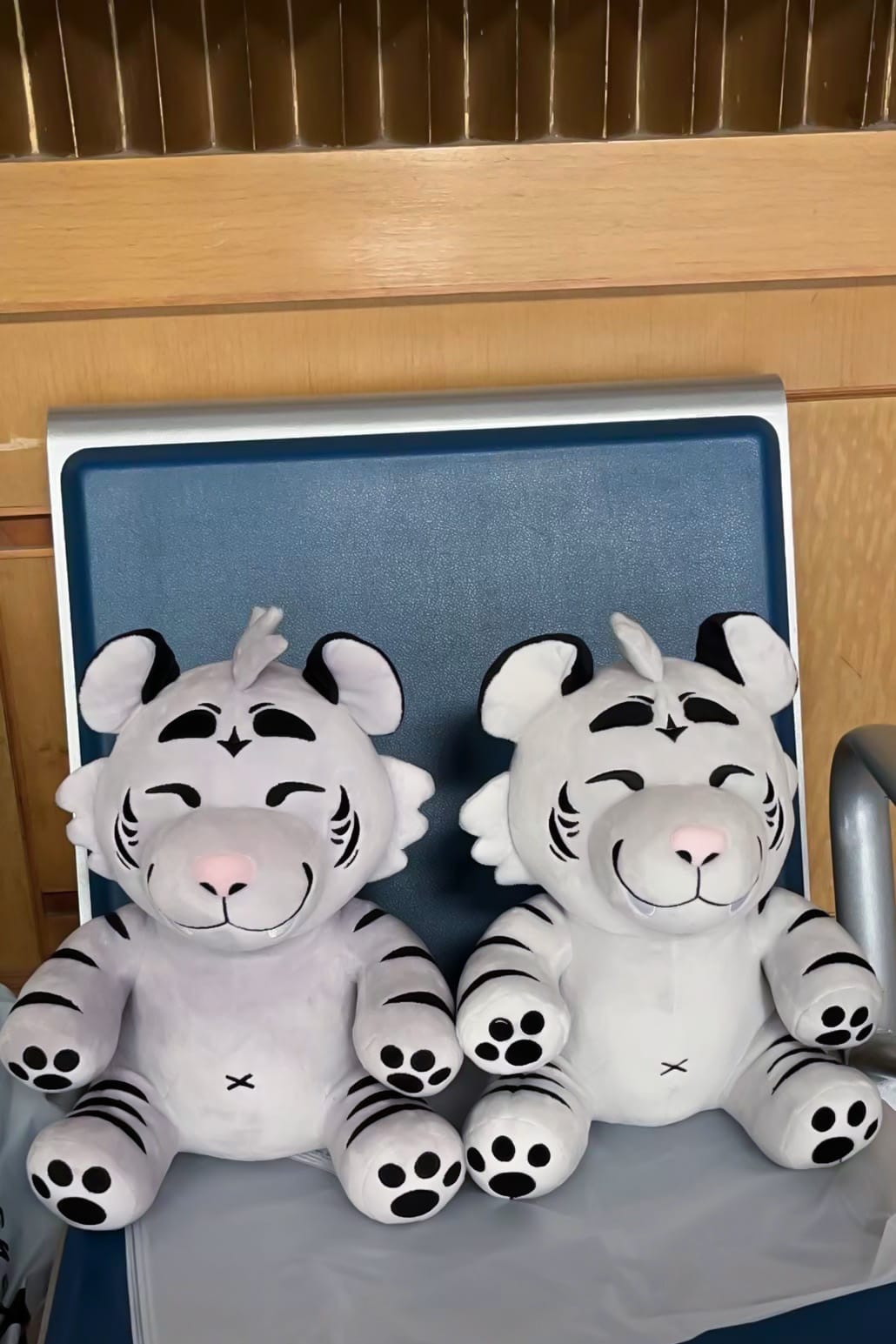
Dave New Pre-Production Sample v1.0, comparing to our prototype
The Axel team did a better job in stuffing, but their embroidery issue is rather significant. Axel's design includes detailed appliqué work for his stripes, which proved problematic. We also noticed defects in facial embroidery, likely due to incorrect machine speed settings. Further investigation gave us no surprise - they outsourced the embroidery work.
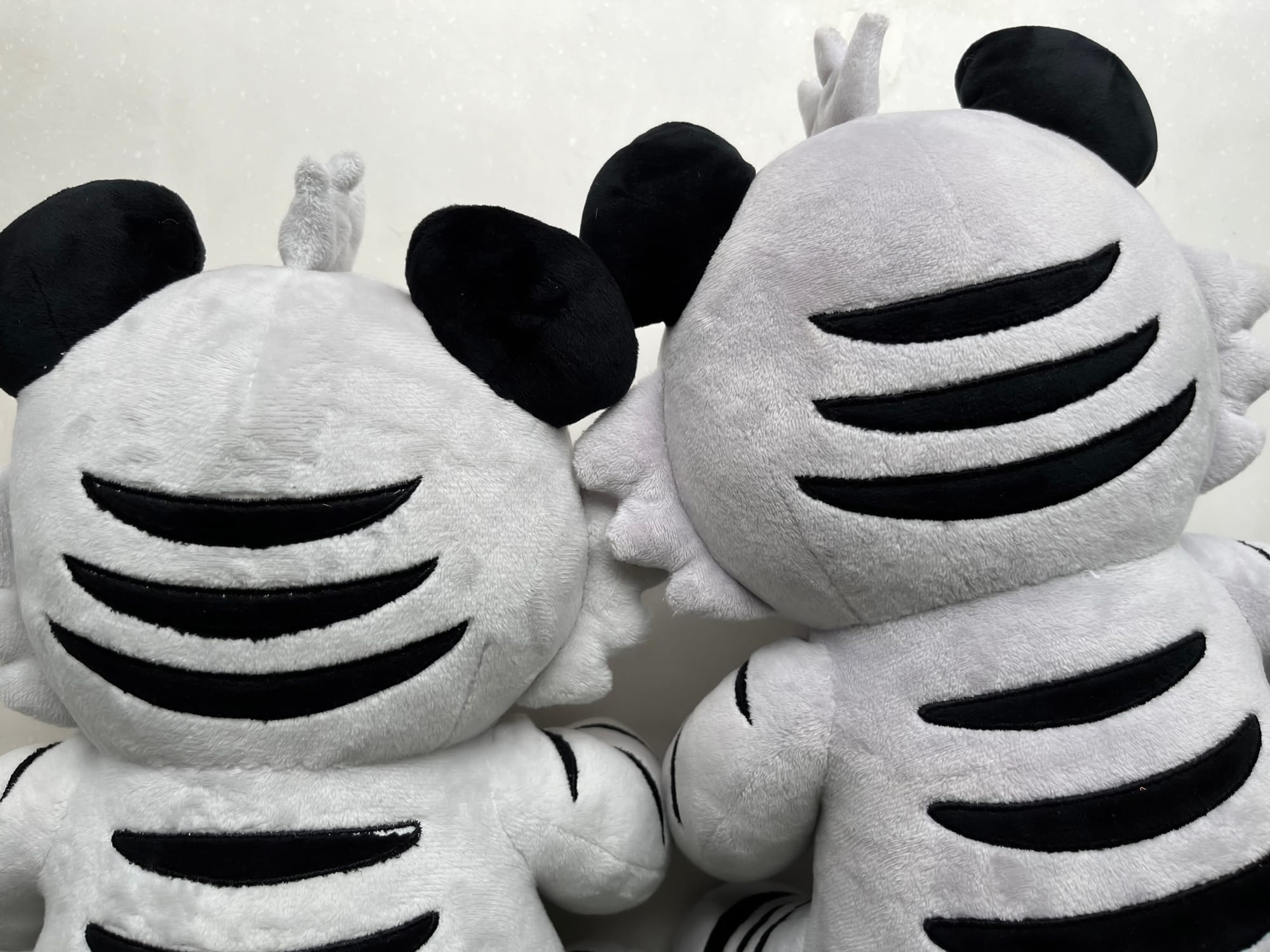
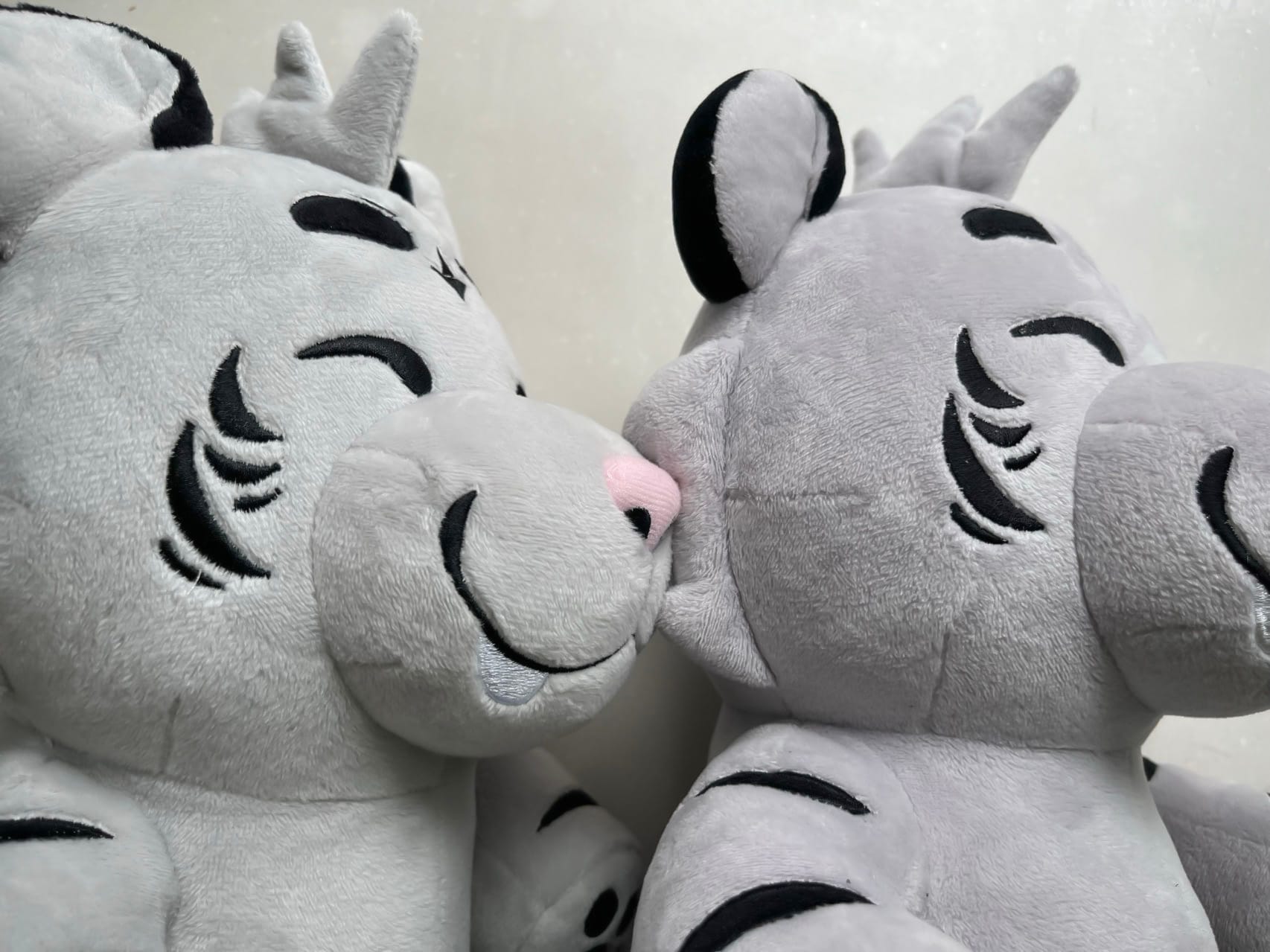
Appliqué and embroidery defects of Axel Pre-Production Sample v1.0, comparing to our prototype
Speaking of which, another thing we’ve learned is how notoriously chaotic the embroidery industry is. Our designer uses an old school Greek software, while most Chinese manufacturers operate Japanese-standard machines with software running the Australian format. It seems to be the status quo for people in this field to encounter a data standard that cannot be adapted to their workflow, and they have developed their own solution: hand tracing the embroidery sequence in their software.
Of course, we couldn't allow this under our strict standards for embroidery accuracy. We soon found that we can output the source file into .dst, the native format by Tajima embroidery machines, which are prevalent in China, along with their knock-off versions. For those interested, this article provides an extensive explanation of embroidery formats.
It may seems puzzling why manual tracing persists over formal training in data formats, but that's just the tip of the iceberg regarding industry primitiveness. We have more bizzare stories to share in the future.
The embroidery process of Dave's Face is being simulated in Wing's MyEditor
For our devoted backstage readers (we believe you are one if you have come this far down the article), here's another secret: we're actively setting up our own workshop to manufacture future plushes in-house. This decision stems from evaluating all costs—tangible and intangible—incurred while training suppliers to meet our standards. Thanks to this experience, we’re now equipped to manage production more steadily and efficiently.
If you’ve purchased our legacy plushes, you’ll notice they don’t even match the quality of the pre-production samples shown in this article. Back then, we were less experienced and had fewer resources to make things perfect, which is why we're retiring the old generation of plushes. One might ask if it’s necessary to elevate the standards to the current level, since, obviously, those old ones were selling too. The thing is, it’s not just about whether the quality is good enough to sell; it’s about how closely we can replicate the design and, further, capture the soul of each character you love, with every penny and all the trust you have ever given us. If one day we eventually deliver these most finely made plushes—hopefully not far from now—do know that it is because of your consistent support to us.
As always, stay tuned.